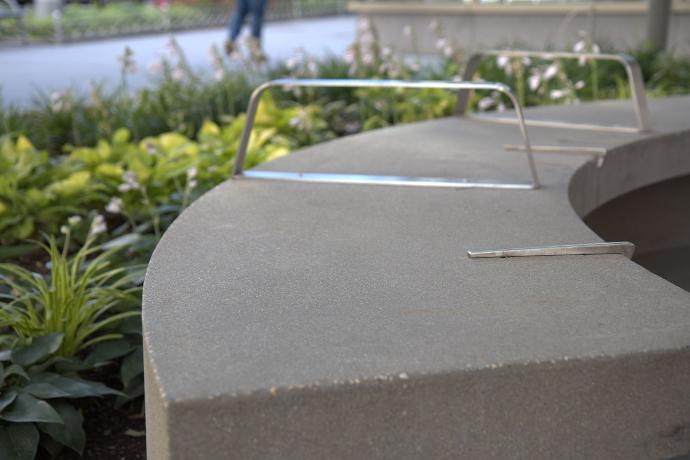
Precast concrete and cast-in-place (CIP) concrete are two different methods of constructing concrete elements in the construction industry. Both methods have their advantages and disadvantages, which are outlined below:
Precast Concrete: Pros:
- Quality control: Precast concrete is manufactured in a controlled factory environment, allowing for precise control over the materials, mix design, curing process, and quality assurance. This can result in consistent high-quality products with fewer variations compared to CIP concrete, which is mixed and cured on-site.
- Faster construction: Precast concrete elements are manufactured off-site and can be transported and installed quickly, reducing construction time and site disruption. This can lead to shorter construction schedules and faster project completion.
- Design flexibility: Precast concrete can be manufactured in various shapes, sizes, colors, and finishes, offering greater design flexibility and customization options for architects and designers.
- Durability: Precast concrete is known for its durability, with high resistance to fire, moisture, pests, and other environmental factors. Precast elements can have a longer service life compared to CIP concrete, resulting in reduced maintenance and replacement costs over time.
Cons:
- Transportation and logistics: Precast concrete elements are typically large, heavy, and require specialized transportation and handling equipment, which can add to the complexity and cost of logistics.
- Site coordination: Precast concrete requires careful coordination with other trades and site conditions, including foundation design, connection details, and handling and erection logistics, which can add complexity to the construction process.
- Limited on-site customization: Once precast concrete elements are manufactured, their design and dimensions are typically fixed and cannot be easily modified on-site, limiting flexibility for last-minute design changes or adjustments.
- Higher initial costs: Precast concrete elements often require upfront investment in molds, equipment, and facilities for manufacturing, which can result in higher initial costs compared to CIP concrete, especially for small-scale projects.
Cast-in-Place Concrete: Pros:
- Site adaptability: CIP concrete can be poured and formed on-site, allowing for greater adaptability to site conditions, changes in design, and modifications during construction.
- Site control: CIP concrete allows for greater control over the concrete mix, placement, and curing process on-site, which can be advantageous in certain situations where site-specific conditions or requirements need to be addressed.
- Lower initial costs: CIP concrete typically requires lower upfront investment in molds, equipment, and facilities compared to precast concrete, making it more cost-effective for small-scale projects or projects with changing design requirements.
- Simplified logistics: CIP concrete eliminates the need for transportation and handling of large precast elements, which can simplify logistics and reduce transportation costs.
Cons:
- Quality control challenges: CIP concrete is mixed and cured on-site, which may result in variations in materials, mix design, curing, and quality assurance, leading to potential inconsistencies in the final product.
- Longer construction time: CIP concrete requires more time for formwork installation, concrete placement, curing, and removal of formwork, which can result in longer construction schedules compared to precast concrete.
- Limited design flexibility: CIP concrete may have limitations in terms of design flexibility and customization compared to precast concrete, as formwork may restrict the complexity of shapes, sizes, colors, and finishes that can be achieved.
- On-site disruptions: CIP concrete construction can create more on-site disruptions due to noise, dust, and other construction activities, which may impact nearby activities, occupants, or the environment.
In summary, both precast concrete and cast-in-place concrete have their advantages and disadvantages, and the selection of the appropriate method depends on the specific requirements of the project, including design, schedule, budget, and site conditions. When it comes time to decide if Precast or CIP is best for you, take the time to research each and see what works best for your job.